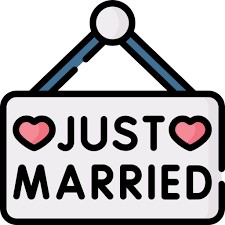
Lean is a philiosophy, a culture and a set of methodologies that focus on improving the value to customers of the products and services they receive.
How do we do this ?
By continuously examining the processes or value streams that supply the customer, with a view to identifying and eliminating waste.
This leads to reduced leadtimes, lower inventory, greater productivity, more capacity, greater flexibility and happier customers.
Industry 4.0 or the 4th revolution to industrial manufacture, sees the incorporation of digital technologies at machine and system level. Smart sensors, big data analytics, artificicial intelligence , cyber physical systems and process simulation are just some of the technologies that will facilitate smart factories to be more efficient, productive and adaptive to customer demands.
So does that mean that Industry 4.0 will effectively do away with LEAN ?
Not so say the experts. In fact Industry 4.0 will truly enable the Lean Enterprise and empower people to improve their processes.
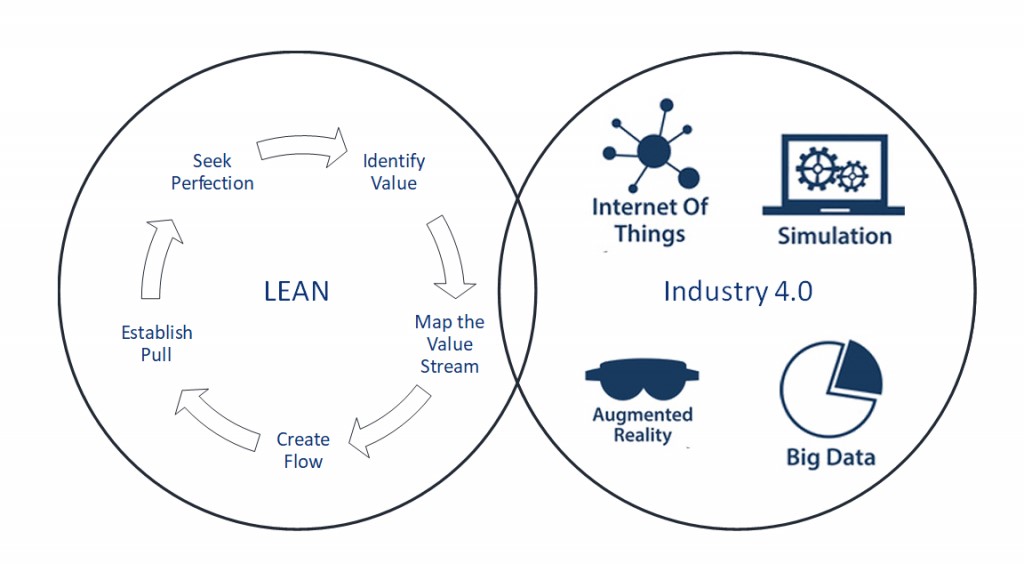
How might this happen ?
Clarity on Value Stream Performance
Central to the principles of Lean is to map the process (also known as the value stream). These are all the process steps with associated material and information flows that define the supply of the product or service. The value stream flows from customer request to customer receipt of the product or service.
This map is used to identify where potential waste exists in the process and where improvements in efficiency can be made. Completing the map involves firstly walking the process and manually recording the data and the inventory associated with each step . This can be time consuming.
Also although the value stream map is a powerful depiction of the process, it is only a snapshot of the process at a point in time. Customer demand varies, inventory varies, mahine efficiencies vary.
Industry 4.0 can provide real time data on customer demand, machine performance and inventory ( e.g. by using RFID). This can allow for more dynamic and quicker optimisation of the value stream to minimise waste.
Quicker problem Solving
In order to identify the causes of particular inefficiencies or defects in the process, we need to gather data on the issue and carry out analysis to establish the root cause. Often this can take time and may require planning of data collection and use of statistical analysis tools.
Industry 4.0 can provide rapid real time data on machine performance and quality metrics. Smart sensors can provide information on component wear. Self diagnostics on machines can facilitate quicker repairs. Some machines will have the capability to auto repair or change over to other components or devices.
Virtual and Augmented Reality will allow for remote diagnosis of problems and speedier resolution.
Solving process problems may require examining large data sets from a variety of sources taken over periods of time. Questions may be asked such as:
Why did this happen ?
Will it happen again ?
What will happen if we make this change ?
Data analytics can facilitate this analysis of these data sets to resolve the problem.
Enlightened Experimentation
A key element of Lean is identifying potential improvements in the process, designing solutions and piloting these solutions. Data on the pilot is gathered and analysed to prove that the solution works before rolling out the full implementation.
In a true Lean Enterprise there is a culture of identifying and pilot testing improvements. We call this “enlightened experimentation”. All personnel are encouraged in this regard.
However this “experimentation “ takes time and can be challenging, particularly in regulated environments.
This process can be greatly helped by implementing a digital twin.
What is a digital twin in manufacturing?
A digital twin is a virtual representation of a system, such as a process like product design or a piece of manufacturing equipment, a production line or an entire factory.
The digital twin can be used to find potential problems and areas to optimise before the physical change is made saving time and money.
Optimising Maintenance Strategies
Overall Equipment Effectiveness (OEE) is a commonly used metric in manufacturing operations. It combines the metrics of
- Availability
- Productivity and
- Quality
The success of a maintenance strategy can be seen in the level of losses that contribute to each of these metrics. It is of vital importance to the manufacturing operation that the correct maintenace strategy is implemented.
A major factor in strategy implementation will be the provision of real time data from machines , systems and smart sensors. Predictive maintenance based on real time, condition monitoring of assets will be made easier.
The use of data analystics to identify and predict potential failure modes will expand and will be simplified.
Autonomous maintenance – the ability of process operators that do not have technical expertise, to carry out maintenance interventions, will be greatly aided by the ability of machines to self- diagnose faults.
Continuous Improvement Programmes
The roll out of Lean and Six Sigma as part of a programme of contnuous improvement requires a big commitment from the business and staff. Time and resource is taken up in identifying and implementing improvement projects.
Often programmes that kick off with fanfare and best intentions can run into problems maintaining momentum. Improvements can become more difficult to identify. The resource commitment to data gathering, data analysis and piloting solutions can be more difficult to justify.
Industry 4.0 technologies can help embed a Continuous improvement programme by making the process slicker and removing the chore of data retieval and analysis.
Systems improvements can be iterated and scaled more easily.
Summary:
So for now at least the manufacturing environment will continue to produce products in processes that can always be improved upon by people asking questions such as “Why ?” and “Why not ?”
Industry 4.0 will undoubtedly assist in identifying the answers and pointing to other questions that we hadn’t even thought of.
Lean and Industry 4.0 are complementary. Their relationship will blossom and grow. Their perfect marriage will bring forward the new paradigm of “Lean 4.0” and a new era in manufacturing.
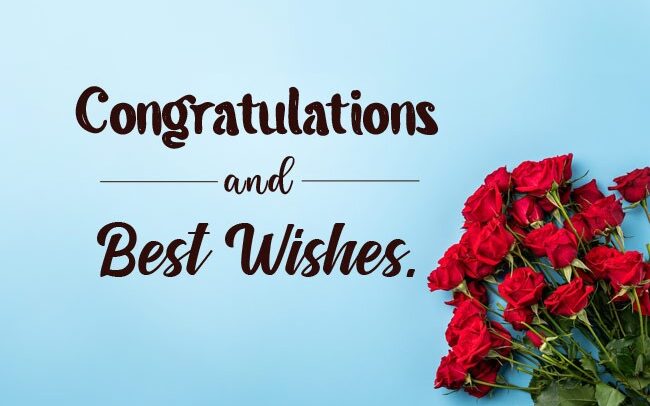